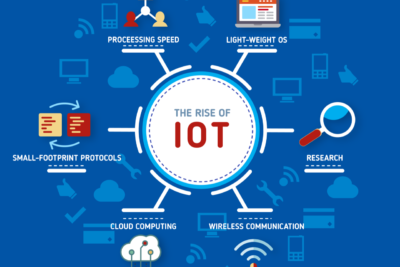
Cuáles son las ventajas de la programación PLC frente a otros métodos de control
hace 4 semanas
Los PLCs, o controladores lógicos programables, se han convertido en una parte integral de la automatización industrial. Estos sistemas de control informáticos han reemplazado gradualmente a los relés electromecánicos y ofrecen una solución más eficiente y versátil para controlar y monitorear procesos en diversas industrias. Los PLCs permiten configurar y programar diferentes tareas y operaciones, lo que los hace extremadamente flexibles y adaptables a diferentes necesidades. En este artículo, exploramos los beneficios clave de la programación PLC y cómo ha revolucionado la industria.
- ¿Cómo funciona un PLC y por qué es tan utilizado en la industria?
- Principales ventajas de elegir un PLC para sistemas de control
- Características y componentes clave de un PLC
- La programación PLC: ¿cómo se realiza y qué beneficios ofrece?
- Evolución y expansión de los PLC en la automatización industrial
¿Cómo funciona un PLC y por qué es tan utilizado en la industria?
Los PLCs funcionan mediante la interacción de componentes clave, como la unidad de procesamiento central (CPU), los módulos de entrada y salida (I/O), la fuente de alimentación y el dispositivo de programación. Estos componentes trabajan en conjunto para recibir datos de entrada, procesarlos y activar las salidas correspondientes según la programación configurada.
El PLC recibe señales de entrada provenientes de sensores, interruptores u otros dispositivos que monitorean el estado de un proceso o sistema. Estas señales son procesadas por el CPU, que las compara con las instrucciones programadas para determinar las acciones a tomar. Una vez que se ha tomado una decisión, el PLC activa las salidas correspondientes, como motores, válvulas o dispositivos de control. Este proceso de entrada-procesamiento-salida se repite de manera continua para garantizar un control preciso y eficiente del sistema.
La utilización de PLCs en la industria se debe a varias razones. En primer lugar, los PLCs son altamente confiables, lo que los hace ideales para entornos industriales exigentes. Están diseñados para soportar condiciones extremas, como vibraciones, temperaturas extremas y ruido eléctrico, sin dejar de funcionar de manera confiable. Además, los PLCs son altamente flexibles y pueden adaptarse fácilmente a diferentes requerimientos y cambios en el proceso de producción. Esto se debe a que los PLCs pueden ser programados para realizar diferentes tareas y operaciones, sin la necesidad de reemplazar componentes físicos, lo que los convierte en una opción rentable y eficiente.
Principales ventajas de elegir un PLC para sistemas de control
1. Flexibilidad y adaptabilidad
Uno de los principales beneficios de la programación PLC es su flexibilidad y adaptabilidad. Los PLCs pueden ser programados para realizar una amplia variedad de tareas y operaciones, lo que los hace altamente versátiles en entornos industriales. Pueden controlar y monitorear diferentes procesos, como el control de motores, la regulación de temperatura, el control de nivel de líquidos y muchas otras aplicaciones industriales. Además, los PLCs pueden ser reprogramados fácilmente para adaptarse a cambios en el proceso de producción o para añadir nuevas funcionalidades.
2. Facilidad en la corrección y modificación de programas
La programación PLC ofrece una gran facilidad para corregir y modificar programas. Cualquier cambio o corrección que se desee realizar en el programa del PLC se puede hacer de forma rápida y sencilla, sin la necesidad de reemplazar o reconfigurar componentes físicos. Esto permite una mayor eficiencia en el proceso de producción, ya que no es necesario detener la producción para realizar cambios en el programa. Además, la programación PLC permite realizar pruebas y simulaciones virtuales antes de implementar los cambios en el proceso real, lo que garantiza una mayor precisión y evita posibles errores.
3. Fiabilidad y durabilidad
Los PLCs son conocidos por su fiabilidad y durabilidad en entornos industriales. Están diseñados para soportar condiciones adversas, como vibraciones, altas temperaturas y ruido eléctrico, sin afectar su rendimiento. Además, los PLCs cuentan con redundancia de software y hardware, lo que garantiza que el sistema siga funcionando en caso de fallas o averías. Esto se traduce en una mayor confiabilidad y disponibilidad del sistema, evitando posibles paradas de producción y minimizando el tiempo de inactividad.
4. Fácil comunicación con otros dispositivos
Los PLCs están diseñados para funcionar en sistemas de control distribuido, lo que implica que pueden comunicarse fácilmente con otros dispositivos y sistemas. Esto permite la integración de diferentes componentes y sistemas, como sensores, actuadores, pantallas de visualización y otros PLCs. La comunicación entre los dispositivos se realiza a través de protocolos estándar de comunicación, como Modbus, Profibus, Ethernet/IP, entre otros, lo que garantiza una fácil interconexión y compatibilidad entre diferentes equipos y sistemas.
Características y componentes clave de un PLC
Los PLCs constan de varios componentes principales que permiten su correcto funcionamiento. Estos componentes incluyen:
1. Unidad de procesamiento central (CPU)
La CPU es el cerebro del PLC y es responsable del procesamiento de datos y la ejecución de las instrucciones programadas. La CPU interpreta y ejecuta secuencialmente las instrucciones para controlar el sistema. La CPU también maneja las comunicaciones con otros dispositivos y sistemas externos.
2. Módulos de entrada y salida (I/O)
Los módulos de entrada y salida son responsables de la conexión del PLC con el mundo exterior. Los módulos de entrada reciben las señales de entrada, como las provenientes de sensores, y las envían a la CPU para su procesamiento. Los módulos de salida activan las salidas del PLC, como motores, válvulas u otros dispositivos, según las instrucciones de la CPU.
3. Fuente de alimentación
La fuente de alimentación suministra energía eléctrica al PLC y a sus componentes. La fuente de alimentación debe ser adecuada para la operación del PLC y debe proporcionar una energía estable y confiable para garantizar el correcto funcionamiento del sistema.
4. Dispositivo de programación
El dispositivo de programación es utilizado para configurar y programar el PLC. Puede ser una computadora personal con un software de programación específico o un dispositivo de programación portátil. El dispositivo de programación permite al usuario ingresar las instrucciones y configuraciones necesarias para controlar y monitorear el sistema.
La programación PLC: ¿cómo se realiza y qué beneficios ofrece?
La programación de un PLC se realiza utilizando lenguajes específicos, como Ladder Logic o Diagrama de Bloques de Funciones (FBD). Estos lenguajes son visuales y se asemejan a esquemas eléctricos, lo que facilita su comprensión y configuración.
Ladder Logic
Ladder Logic es uno de los lenguajes de programación PLC más utilizados. Se basa en símbolos gráficos que representan diferentes componentes y funciones. Estos símbolos se colocan en una línea horizontal llamada "rung", que representa una condición o acción específica. Estas rungs se organizan en redes, que representan diferentes etapas u operaciones del programa. Ladder Logic es especialmente útil para programar secuencias lógicas y de temporización.
Diagrama de Bloques de Funciones (FBD)
El Diagrama de Bloques de Funciones (FBD) es otro lenguaje de programación PLC utilizado comúnmente. Se basa en bloques gráficos que representan diferentes operaciones o funciones. Estos bloques se conectan entre sí mediante líneas, que representan la secuencia de ejecución del programa. FBD es especialmente útil para programar operaciones matemáticas y lógicas más complejas.
La programación PLC ofrece varios beneficios clave. En primer lugar, la programación visual facilita la comprensión y configuración del programa, lo que reduce los errores y simplifica el proceso de programación. Además, la programación PLC permite realizar pruebas y simulaciones virtuales antes de implementar el programa en el sistema real, lo que garantiza un control preciso y evita posibles fallos o problemas. Además, la programación PLC permite una mayor flexibilidad y adaptabilidad, ya que los programas pueden ser modificados y actualizados fácilmente sin la necesidad de reemplazar componentes físicos.
Evolución y expansión de los PLC en la automatización industrial
Desde su introducción en la industria hace varias décadas, los PLCs han experimentado una rápida evolución y expansión. Inicialmente, los PLCs se utilizaban principalmente para controlar y monitorear procesos simples, como el encendido y apagado de motores. Sin embargo, con los avances en la tecnología y la programación, los PLCs se han vuelto mucho más potentes y versátiles.
En la actualidad, los PLCs pueden controlar y monitorear una amplia variedad de procesos industriales. Esta expansión se ha logrado a través del desarrollo de nuevos módulos de entrada y salida, que permiten la conexión con diferentes tipos de sensores y actuadores. Además, los PLCs actuales son capaces de realizar cálculos matemáticos más complejos y funciones lógicas avanzadas, lo que amplía aún más sus capacidades.
Además de su evolución en términos de capacidades, los PLCs también se han expandido en términos de su uso en diferentes áreas de la automatización industrial. Hoy en día, los PLCs se utilizan no solo en el control de procesos, sino también en el control de movimiento, sistemas de control distribuido y conexiones en red. Estas aplicaciones más avanzadas permiten un control más preciso y eficiente de los sistemas industriales, lo que contribuye a una mayor productividad y calidad en la producción.
La programación PLC ofrece una serie de beneficios clave que hacen que estos sistemas de control informático sean ampliamente utilizados en la industria. La flexibilidad y adaptabilidad de los PLCs, su facilidad para corregir y modificar programas, su fiabilidad y durabilidad, y su fácil comunicación con otros dispositivos son solo algunas de las ventajas que hacen que la programación PLC sea una opción preferida en la automatización industrial. A medida que los PLCs continúan evolucionando y expandiéndose, es probable que su papel en la industria siga creciendo y contribuyendo a la eficiencia y productividad de los procesos industriales.
⭐️ Si quieres saber más de otros artículos parecidos a Cuáles son las ventajas de la programación PLC frente a otros métodos de control puedes visitar nuestra categoría Variados. Te esperamos dentro 👍
Deja una respuesta
Entradas de Interes